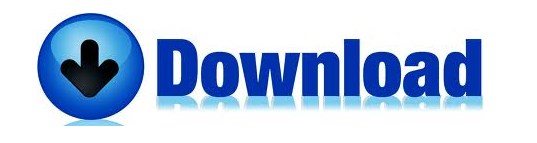

There are also other formulations that are sometimes called generalized plane strain. When you select the generalized plane strain option in COMSOL Multiphysics, you have the possibility to select between the pure axial extension assumption and the inclusion of bending. The values of a, b, and c are determined by the assumption that no net axial force or bending moments act on the cross section that is, the ends are free. If the parameters a and b are also included, the extrusion is also allowed to bend with a constant curvature. Physically, this means that the long object is allowed to expand axially in the z direction. In a common interpretation of generalized plane strain, only the coefficient c is used. There are, however, three new unknowns, a, b, and c. Thus, there are still only two components of the displacement field, u and v, to be solved for. In the z = 0 plane, where the analysis is performed, w is zero. The assumptions are simple: No displacement in the z direction. This is a fundamental difference from the 2D approximations for most other physics fields. The object does, however, not have to be “long” in the z direction. This is also the formulation that conceptually has the best correspondence to 2D formulations in other physics fields. A state of plane strain will exist in an object that is constrained in the z direction between two rigid walls. Plane strain is the only one of the 2D solid mechanics formulations that does not contain approximations. It should be noted that if there is no coupling between in-plane and out-of-plane action (for example, when Poisson’s ratio is zero for a linear elastic material), then all formulations will be identical. The displacements in the xy-plane are called u and v respectively, and w is the displacement in the z direction. In the following section, it is assumed that 2D means the xy-plane, and that z is the out-of-plane direction. Different 2D Formulations for Solid Mechanics This will be discussed in more detail below. The thickness change is a result that can be computed a posteriori, in case you are interested. However, that does not directly affect the solution to the 2D problem. For example, it will get thinner if you stretch it. The thin plate will, in general, deform in the transverse direction. In the case of solid mechanics, there is also an effect in the out-of-plane direction. Similar reasoning can be applied to many other physical phenomena. Thus, a 2D approximation for heat transfer in thin plates is more difficult. Then, the temperature gradient in the thickness direction is important. In that case, convection and radiation from the large surfaces will occur in the out-of-plane direction. What is then so special with solid mechanics that makes this possible?Ĭonsider analyzing the same plate for heat transfer. We can, for example, consider a thin, flat plate, loaded only in its plane, as two-dimensional. In the field of solid mechanics, there are more possibilities for 2D states than a very long extrusion.
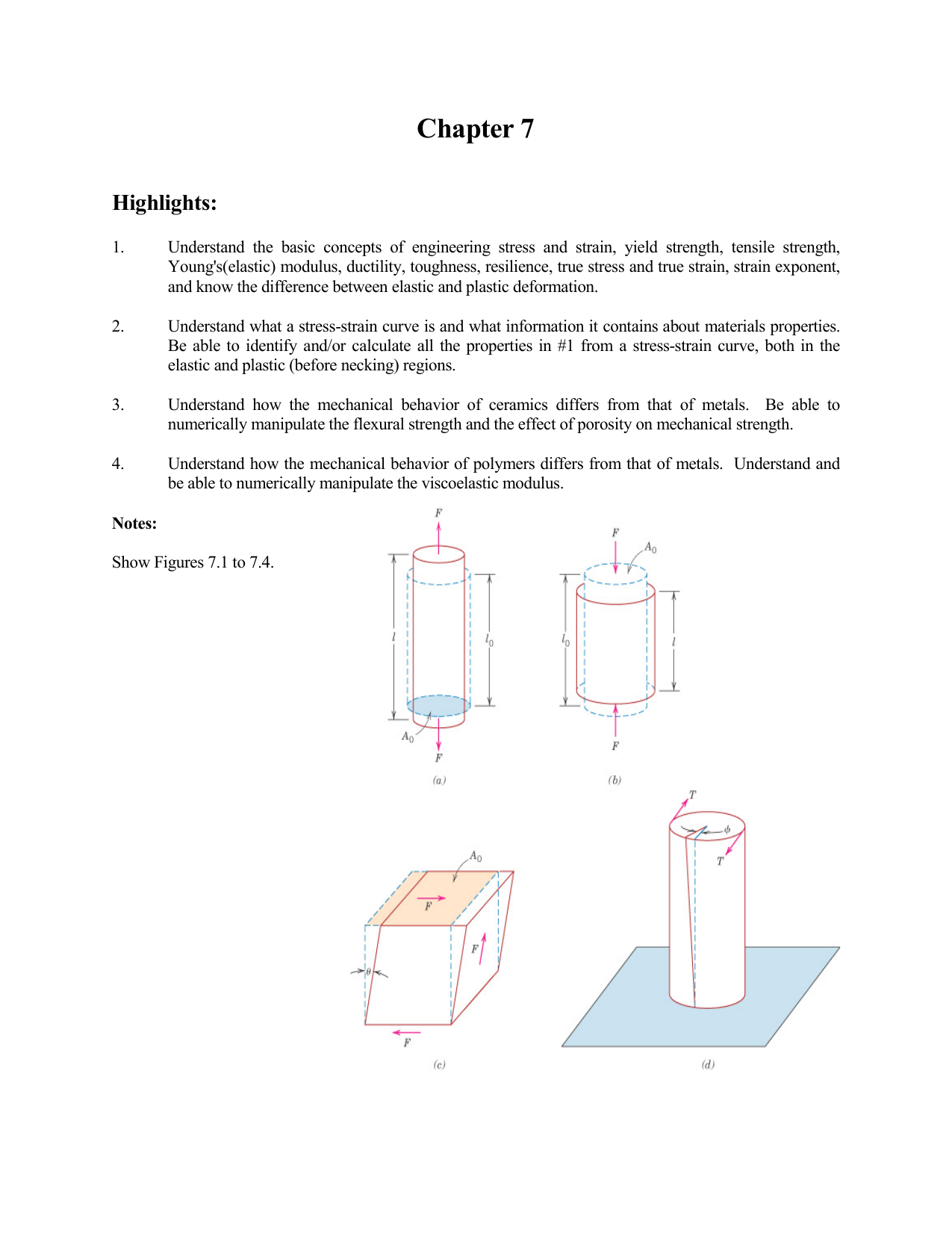
The cross section is representative of a situation in which the cables are long, straight, and parallel. The electric potential (color code) and electric field (arrows) around two long cables with different potentials, as computed in 2D. Sufficiently far from the ends, the fields depend only on the location in this cross-sectional plane.” For most physical problems, this is the idea: In a 2D approximation, we study a cross section of a long, straight object, ignoring end effects. When we, for example, study the electromagnetic fields around a cable cross section in 2D, we are actually saying: “This cable is straight and long. There is not much in real life that is actually two-dimensional. In this blog post, we take a look at when and how it is possible to study problems in the field of solid mechanics using 2D formulations.

Still, in engineering analysis, it is common to use 2D approximations to save both modeling and computational resources. We live in a three-dimensional world - or maybe four-dimensional, if you consider space–time.
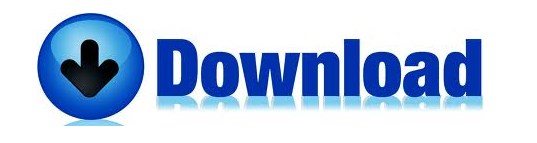